Sponsored article
How to save on energy costs in welding processes?
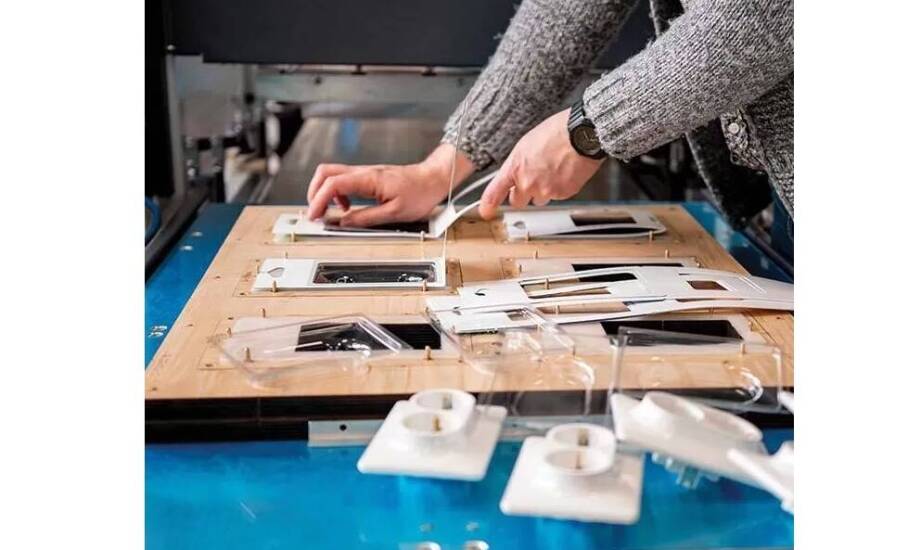
Energy saving in welding processes is becoming increasingly important, especially in the face of rising costs. Energy efficiency is crucial for industry, affecting the competitiveness and profitability of companies. High energy expenditure can have a negative impact on production, so it is worth seeking solutions to reduce energy consumption. Read on to find out more about welding savings!
Types of welders and their energy efficiency
Various types of welders are available on the market, including automatic machines that significantly affect energy consumption. Choosing the right equipment can help to reduce operating costs. Energy-efficient welders use less energy during operation, resulting in lower electricity bills. In addition, modern technology allows precise control of the welding process, which minimises energy loss. Investing in an automatic welder can be beneficial both in terms of saving money and improving the quality of the operations. It is worth considering this aspect when choosing equipment to maximise the potential of modern solutions.
Techniques to improve energy efficiency
In order to increase the energy efficiency of welding processes, it makes sense to use a variety of techniques and methods. Above all, machine parameters, such as welding time and temperature, must be precisely optimised. It is also a good idea to invest in modern equipment, such as an automatic welder, which has higher energy efficiency. Another aspect is the organisation of work – proper planning of processes and training of employees can contribute to significant savings. Regular maintenance of equipment plays an important role in maintaining high energy efficiency.
Importance of equipment maintenance
Zemat Technology Group stresses that regular maintenance, including of automatic welders, is key to maintaining energy efficiency. Neglecting inspections can lead to breakdowns and increased energy consumption. It is worth developing a schedule that takes into account both regular maintenance and the replacement of worn components. This ensures that the machines run efficiently and economically. It is also important to monitor the condition of the equipment and respond to any problems before they become more serious failures.
Innovations in energy saving
In recent years, many companies have invested in state-of-the-art technology regarding energy savings during welding processes. An example of this is the automatic welder, which, thanks to its advanced control algorithms, consumes significantly less energy than traditional equipment. Case studies of companies that have implemented such innovations show that savings can be as high as 30% compared to previous solutions. Companies offering comprehensive support in the field of energy consultancy and machine servicing are worth considering. In this way, you can avoid mistakes when selecting the right solutions and maximise their savings potential.